31.05.2021
Eine Reise durch die Zeit – der Flottweg Separator und seine Geschichte
Als einer der Weltmarktführer für Trenntechnik bietet Flottweg für die verschiedensten Anwendungsbereiche Lösungen für die mechanische Fest-Flüssig-Trennung an. Neben Komplettlösungen und Produkten, wie dem Flottweg Dekanter, gehört der Flottweg Separator schon seit über 20 Jahren zur Flottweg Produktpalette. In unserem Interview erzählen Frank Giegler, Verfahrenstechniker bei Flottweg, und Christoph Hobmeier, Entwicklungsingenieur bei Flottweg, die spannende Geschichte des Flottweg Separators.
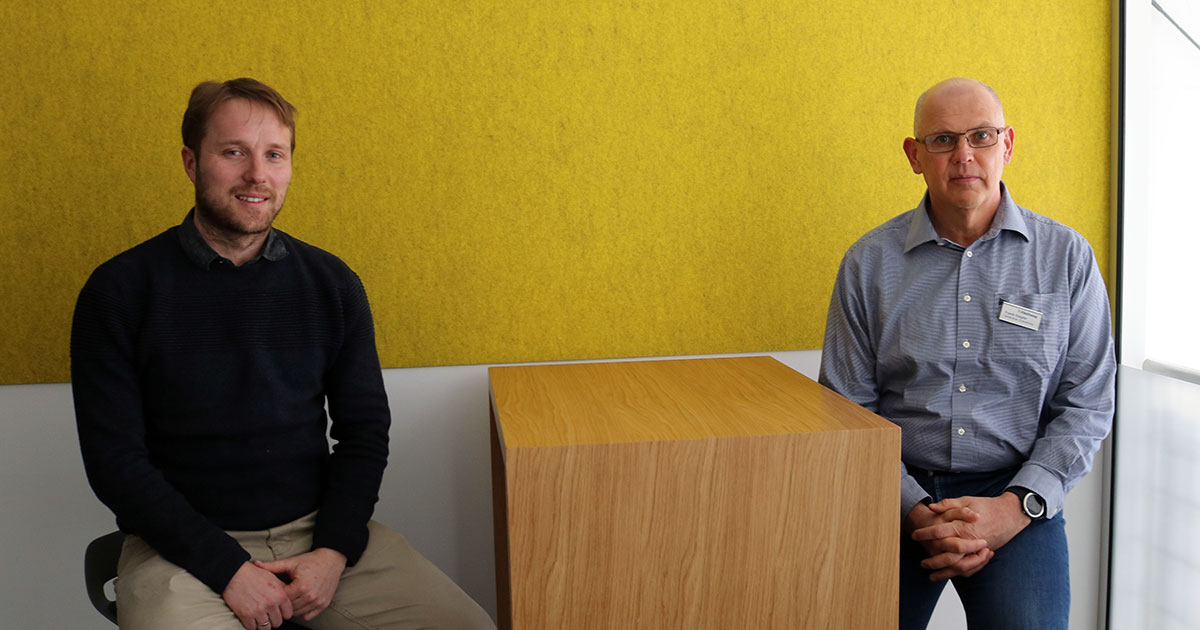
Der Separator ist schon seit über 20 Jahren ein Teil der Flottweg Produktpalette. Wie hat das alles angefangen?
Frank:
Die Geschichte der Separatoren bei Flottweg ist etwas länger als die meisten glauben. In der 60er/70er Jahren gab es schon die ersten Überlegungen, selber einen Separator zu entwickeln. Ende der 80er Jahre hat die Zusammenarbeit von Flottweg mit unserer jetzigen Tochter Veronesi aus Bologna, Italien, angefangen. Flottweg hat mit den Separatoren von Veronesi das Produktportfolio erweitert, um ein nachgeschaltetes Trennaggregat, nach dem Dekanter, anbieten zu können. Da die Fertigungsmaschinen bei Veronesi für die geplante AC2500 nicht ausreichten, wurde 1998 entschieden, die Produktion nach Vilsbiburg zu verlagern. Damit hat meine Geschichte bei Flottweg angefangen. Die AC2500 wurde entwickelt, um den Markt für Fruchtsaft und Wein zu erobern. Ein Jahr später und nach Überwindung einiger Hürden drehte sich der Prototyp in unserem Technikum. In den Jahren 1999 und 2000 wurde die Maschine weiter verbessert. Im Jahr 2001 war es endlich so weit: Unser jetziger Sprecher des Vorstands, Herr Fritz Colesan, verkaufte den ersten bei Flottweg gebauten Separator an eine Weinkelterei, bei der dieser seit September 2001 seinen Dienst verrichtet.
Was hat sich von den ersten Anfängen bis heute verändert?
Christoph:
Seitdem ist die Produktpalette stark erweitert worden. Gestartet haben wir mit der AC2500. Als zweiter Schritt wurde die AC2000 eingeführt. Diese ist etwas kleiner und etwa für den halben Durchsatz geeignet. Dann hat man weiter nach unten entwickelt – die AC1500 und schließlich die AC1200. Es wurden sozusagen immer mehr Maschinengrößen in das Portfolio aufgenommen. Zudem sind immer mehr Produktvarianten der Separatoren erstellt worden. Begonnen wurde mit einem Klärer für Fruchtsaft. Dann haben wir nach und nach verschiedene 3-Phasen-Separatoren entwickelt. Anschließend sind Klärer mit hydrohermetischer Abdichtung, speziell für Bier, hinzugekommen. Es folgten Separatoren verschiedenster Ausführungen, zum Beispiel mit höherer Korrosionsbeständigkeit, für höhere Feststoffdichten oder für Produkte mit höherer Viskosität. Es sind Ausführungen mit elektronischen Komponenten und EX-Zertifizierungen für den Einsatz im explosionsgefährdeten Bereich entwickelt worden und wir haben sogar inertisierte Ausführungen entwickelt. Diese dürfen nicht nur in einem explosionsgefährdeten Bereich aufgestellt werden, sondern es können auch explosionsgefährdete Produkte damit verarbeitet werden. Somit ist das Produktportfolio ausgehend von einem großem Klärer stetig erweitert worden. Heute haben wir Baukästen, aus denen sich circa 70 sinnvolle Maschinenausführungen ergeben.
In welchen Anwendungsbereichen kommen die unterschiedlichen Maschinenausführungen zum Einsatz?
Frank:
Der freie Überlauf auf Öl- oder Fettseite wird hauptsächlich bei hohen Temperaturen eingesetzt, wie beispielsweise bei Tierfett oder Fischöl. Der freie Überlauf auf Wasserseite wird beispielsweise für Olivenöl eingesetzt. Die Hydrohermetik setzen wir größtenteils bei Bier ein oder aber zum Teil auch bei Wein. Das kommt ganz auf die Kundenanforderung an.
Mittlerweile haben wir unsere Separatoren in vielen Anwendungen in Betrieb. Der erste Separator arbeitet, wie schon gesagt, seit 20 Jahren in einer Weinkelterei. Danach folgten Separatoren zum Verarbeiten von Fruchtsaft, Zitruspektin, Kaffee, Koffeinaufbereitung, Tee, Sojamilch, Zitrusöl, Orangensaft, Apfelpektin, Bier, Molke, Olivenöl, Fischöl, Biodiesel, Tierfett, Trinkalkohol, Algenernte, Altölaufbereitung und vielem mehr.
Christoph:
Im Prinzip ist es so: Wir haben aktuell vier verschiedene Baugrößen für unterschiedliche Durchsatzbereiche. Diese sind im Wesentlichen vom Anwendungsbereich unabhängig. Die ganzen anderen Geschichten – was für eine Maschinenausführung ich nehme, einen Klärer oder einen Trenner, ob ich eine Maschine wähle mit höherer Korrosionsbeständigkeit oder mit Standardmaterial, ob ich eine Ausführung nehme für höhere Feststoffdichten und so weiter, das sind eigentlich lauter Modifikationen oder Varianten, die vom Produkt getrieben sind. Hier haben wir die Maschine angepasst, damit diese mit den verschiedensten Produkten, unabhängig von der Feststoffdichte oder dem Korrosionsverhalten, umgehen kann.
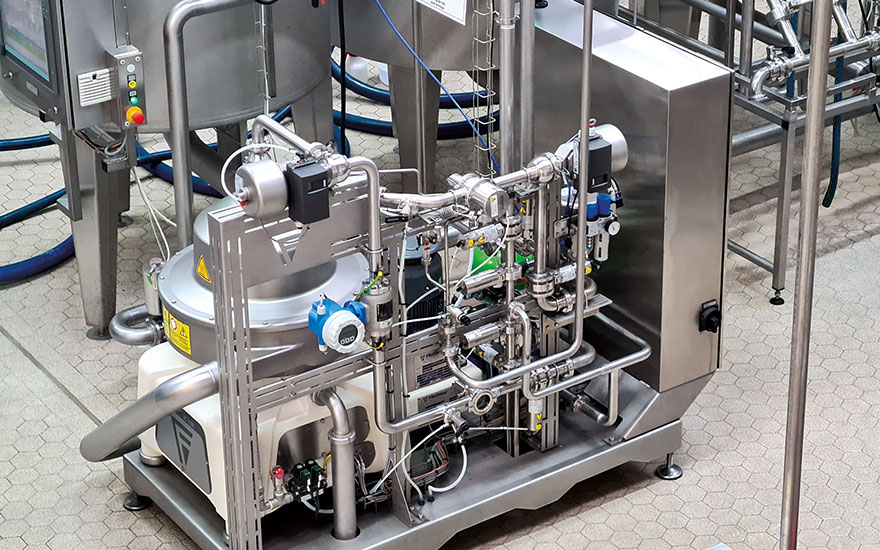
Wie läuft ein Entwicklungsprojekt ab und gibt es dafür ein spezielles Team „Separator“ bei Flottweg?
Christoph:
Offiziell gibt es nur ein Entwicklungsteam für Separatoren in der Entwicklungsabteilung. Das besteht aus mehreren Entwicklungsingenieuren und ist eins von vier Entwicklungsteams bei Flottweg. In einem Entwicklungsprojekt haben wir aber einen stark interdisziplinären Ansatz. Typischerweise sind ständige Projektmitglieder neben der Entwicklung die Konstruktion und die Verfahrenstechnik, die bereits während der Konzeptphase stark mit eingebunden sind. Hier wird geklärt, für welche Produkte die Maschine entwickelt wird und wie das Konzept für die Neuentwicklung aussieht. Der Einkauf, die Arbeitsvorbereitung und die Projektierung sind auch ständige Projektmitglieder in den Entwicklungsprojekten. Dazu kommen noch temporäre Projektmitglieder, die nicht über den kompletten Projektverlauf benötigt werden, die aber dennoch eine wichtige Rolle spielen. Das ist zum Beispiel der Vertrieb, der ganz am Anfang und am Ende des Projektes mit dabei ist, wenn es um die externe Erprobung der Prototypen geht. Die Fertigung und die Montage sind vorrangig am Projekt beteiligt, wenn die Prototypen gefertigt oder montiert werden. Hier sind wir auf das Feedback der Kollegen und deren Mitarbeit angewiesen. Das Controlling und die Dokumentation kommen in bestimmten Projektschritten mit dazu. Das Controlling ist beteiligt, wenn es um das Einplanen der Prototypen geht oder später, wenn es um den Verkauf geht. Die Dokumentation wird eher am Ende des Projekts hinzugezogen, wenn es um das Erstellen der Produktdokumentation geht, damit das Produkt überhaupt im Feld erprobt oder verkauft werden kann. Ein Entwicklungsprojekt erstreckt sich letztendlich fast über die ganze Firma, die im Laufe des Projekts einbezogen wird. Außerdem sprechen wir bei so einem Projekt von einer Dauer von 1-2 Jahren oder sogar von drei Jahren, wenn man etwas ganz Neues macht.
Wie läuft ein Separator-Beschaffungsprozess ab?
Christoph:
Bei normalen Serienmaschinen ist weder die Entwicklung noch die Verfahrenstechnik beteiligt. Es wurden Rahmenbedingungen definiert, die widerspiegeln, welche Durchsatzbedingungen und Produkte bereits erprobt sind. Handelt es sich um solch eine erprobte Anwendung, kann der Vertrieb selbständig Maschinen ordern, in Beschaffung bringen und verkaufen.
Wenn ein Separator bestellt wird, definiert der Vertrieb zusammen mit der Konstruktion die Maschine und übergibt das Ganze an die Auftragslogistik. Diese erstellt einen Fertigungsauftrag für die Montage, woraufhin die Maschine gebaut und abgenommen wird. Die Maschine wird dann entweder an den Kunden geliefert oder geht weiter in unseren Anlagenbau, um dort mit einem Skid, Schaltschrank, etc. komplettiert zu werden.
Wie häufig kommen individuelle Kundenanfragen vor?
Frank:
Das kommt schon häufiger vor, vor allem im Chemie- und Pharmabereich. Das ist der Fall, wenn spezielle Vorgaben erfüllt werden müssen, wie zum Beispiel eine höhere Beständigkeit, eine höhere Dichte oder wenn es um die Qualität der Trennung eines Produktes geht. Hier sprechen wir dann Empfehlungen aus.
Christoph:
Was dahintersteht, sind die sogenannten Machbarkeitsprüfungen. Hier stellt der Vertrieb fest, dass er eine Kundenanfrage hat, die er nicht aus den 70 Maschinenausführungen, die wir zur Verfügung haben, bedienen kann, die aber relativ ähnlich ist. Daraufhin stellt der Vertrieb eine Machbarkeitsanfrage an die Technik. Die Verfahrenstechnik und die Entwicklung schätzen ab, wie hoch der Aufwand ist, um dieser Kundenanforderung zu entsprechen. Anschließend wird entschieden, ob man diesen Aufwand freigibt und dem Kunden eine Zusage geben kann.
Was waren bisher die spannendsten oder außergewöhnlichsten Projekte?
Frank:
Ein wirklich spannendes Projekt war unter anderem bei einer Brauerei in München, wo wir die Maschine getestet haben. Da war es bereits schwierig, die Maschine an Ort und Stelle zu bringen. Wir haben dabei alle gehofft, dass wir sie nicht mehr aus dem tiefsten Keller rausbringen müssen, weil das noch schwieriger geworden wäre als das Reinbringen. Dann haben wir erstmal alle gängigen Biersorten mit dem Separator getestet. Es wurde Vergleichsbier abgefüllt, das mit dem Separator und ohne den Separator verarbeitet wurde. Das wurde dann ein Vierteljahr lang verkostet, um festzustellen, ob eine geschmackliche Veränderung vorhanden ist. Nachdem diese nicht festzustellen war, durfte der Separator erst wieder laufen. Dann hat es nochmal ein Vierteljahr gedauert, bis die Maschine verkauft war und wir im Volksfest mit der Maß darauf anstoßen konnten.
Dasselbe hatten wir auch bei einem Apfelpektinhersteller. Als ich das erste Mal dort war, standen dort ausschließlich Separatoren eines Mitbewerbers. Mittlerweile hat der Kunde nahezu alle Trennaggregate durch Flottweg Maschinen ersetzt.
Christoph:
Von meiner Seite war das spannendste Entwicklungsprojekt die AC1200, weil wir da in vielen Bereichen die Freiheit hatten, neue oder andere Wege zu gehen. Das war eine Maschine, die man von vorne bis hinten neu konstruiert hat und wo das Design und der Aufbau des Separators neu gestaltet wurden. Außerdem wurde hier auch zum ersten Mal dieser interdisziplinäre Ansatz stärker verfolgt. Das war vor allem für mich ein sehr gutes Lernprojekt.
Der Flottweg Separator gilt in manchen Bereichen noch als Newcomer. Woran liegt das?
Christoph:
Generell ist es so, dass wir viele Maschinenausführungen verfügbar haben und bereits in sehr viele Branchen Separatoren geliefert und dort in Betrieb haben. Da wir jedoch erst seit circa 20 Jahren in diesem Geschäftsbereich tätig sind, wohingegen andere Unternehmen schon viel länger dabei sind, sind wir in manchen Bereichen dementsprechend noch der Newcomer.
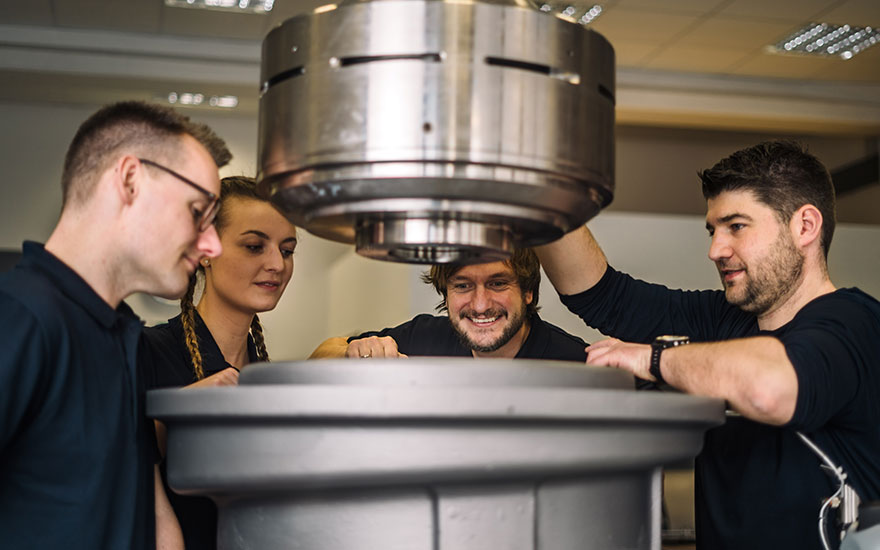
Was zeichnet den Flottweg Separator aus? Was sind unsere Vorteile gegenüber den Mitbewerbern?
Frank:
Unsere Separatoren sind erstmal sehr robust in der Verarbeitung. Außerdem können sie mit Prozessschwankungen sehr gut umgehen. Wie gesagt, der Kunde aus der Pektinherstellung hatte zuvor Separatoren von unseren Mitbewerbern. Dieser Kunde hat seine Leute aus der Instandhaltung gefragt und diese haben sich klar für unseren Separator ausgesprochen. Sie meinten, dass wir deutlich einfacher, günstiger und schneller in der Wartung sind. Und auch die Maschinenbediener des Pektinherstellers meinten, dass unsere Maschine mit Schwankungen oder Störungen im Vorprozess besser zurechtkommt als andere Modelle.
Christoph:
Unsere Maschine ist sehr robust und sehr wartungsfreundlich. Zwei geübte Personen schaffen es innerhalb von einer Stunde, den Separator so weit in seine Hauptkomponenten zu zerlegen, dass man sieht, an welcher Stelle vielleicht ein Problem ist oder um mit dem Austauschen der Teile im Service anfangen zu können. Da sind wir recht zügig unterwegs. Für viele Kunden ist das ein Argument, wenn man schnell und einfach Wartungen durchführen kann und die Maschine schnell wieder zur Verfügung steht.
Zum anderen zeichnen sich unsere Flottweg Separatoren durch ihr Entleerungssystem aus. Dieses bietet neben dem einfachen Aufbau und der einfachen Wartbarkeit noch den Vorteil des SoftShot®, wodurch das Entleerungsgeräusch sehr stark reduziert wird. Die ganze Mechanik dahinter ist wesentlich einfacher als bei vielen Maschinen unserer Mitbewerber, bietet aber trotzdem die Möglichkeit, Teilentleerungen sowie Vollentleerungen auszulösen.
Was erwartet uns in der Zukunft?
Christoph:
Wir haben zurzeit viele interessante Entwicklungsprojekte. Ein Projekt ist zum Beispiel die Überarbeitung der AC1500, die gerade in das Design der AC1200 überführt wird, wobei einige Bauteile und Baugruppen neu gestaltet werden. Dann sind wir kurz davor, die Entwicklung einer neuen Zwischengröße abzuschließen. Das ist die AC1700, welche von der Maschinengröße her zwischen der AC1500 und der AC2000 anzusiedeln ist. Mit dieser neuen Maschinengröße können wir noch gezielter auf die Durchsatzwünsche der Kunden eingehen.
Die Entwicklung eines Düsenseparators ist ein weiteres sehr vielversprechendes Projekt. Hierbei handelt es sich um ein neues Trennaggregat für Flottweg. Wenn wir bisher von Separatoren geredet haben, ging es um selbstentleerende Separatoren, die eine hydraulische Öffnungsmechanik haben. Beim Düsenseparator sind am Trommelumfang eine große Anzahl von Düsen verbaut, durch die der Feststoff ausgetragen wird. Hier finden zurzeit verschiedene Prototypenversuche im Feld statt. Die ersten Erprobungen waren sehr erfolgreich, so dass auch schon die ersten Maschinen verkauft wurden. Darüber hinaus sind wir noch dabei, den Produktbaukasten zu vervollständigen. Zum einen planen wir eine neue Ausführung der AC1500, um höhere Feststoffdichten verarbeiten zu können, zum anderen sind wir dabei, die AC2500 und AC1200exp (inertisiert) zu etablieren. Wir haben also einen ganzen Schwung an interessanten Entwicklungsprojekten.
Frank:
Dazu kommen noch kleine Entwicklungen, wie etwa die Reduzierung des Energieverbrauchs unserer Maschinen oder auch kleine Anpassungsentwicklungen, die über Machbarkeitsanfragen reinkommen.
Christoph:
Im Wesentlichen kann man sagen: Wir runden zum einen unser Produktportfolio ab, wir erweitern es um neue Baugrößen und wir gehen mit dem Düsenseparator sogar ganz neue Wege.
Über unsere Experten
Hobmeier Christoph
Seit 2015 bei Flottweg
Entwicklungsingenieur im MDS (Machine development Separator) -Team
Giegler Frank
Seit 1998 bei Flottweg
Im Versuch angefangen und mittlerweile in der verfahrenstechnischen Entwicklung tätig

Sie möchten mehr über Flottweg erfahren?
Sprechen Sie uns an oder schreiben Sie uns!