07.11.2022
Ausbeute verdoppelt – Flottwegs Tricanter® in der Bioetha-nolproduktion bei Glacial Lakes Energy LLC
Glacial Lakes Energy LLC betreibt in South Dakota, im Nord-Westen der USA, vier Bioethanolanlagen und hat bereits mehr als 20 Jahre Erfahrung in der Bioethanolproduktion. Als Nebenprodukt der Bioethanolherstellung gewinnt das amerikanische Unternehmen zudem Maisöl, das als wertvoller Rohstoff weiterverkauft werden kann. Um die Ausbeute und die Qualität des gewonnenen Maisöls zu verbessern, entschied sich Glacial Lakes Energy LLC in zwei Anlagen für einen Flottweg Tricanter®. Mit der neuen Trenntechnologie ist es gelungen, einen höheren Ertrag zu erzielen sowie ein qualitativ äußerst hochwertiges Öl zu produzieren. Gleichzeitig konnten die Betriebszeiten bei geringerem Wartungsaufwand erhöht werden.
Glacial Lakes Energy betreibt in South Dakota vier Bioethanolanlagen: Aberdeen, Huron, Mina und Watertown. Alle vier Anlagen werden von Geschäftsführer Pat Hogan verwaltet und befinden sich in einem Radius von circa zwei Stunden Fahrzeit. Jedes Werk hat einen Betriebsleiter, Produktionsleiter und Wartungsleiter, die für die individuelle Pflege und den Betrieb der Anlagen verantwortlich sind.
Die Anlage GLE-Watertown wurde im August 2002 in Betrieb genommen und erbrachte eine Nennleistung von ursprünglich 40 Millionen Gallonen im Jahr (MMgy), was rund 150 Millionen Litern jährlich entspricht. Im Jahr 2007 wurde die Anlage erweitert und produziert derzeit mehr als 500 Millionen Liter Bioethanol. GLE-Mina wurde im Juni 2008 zur Produktion von rund 415 Millionen Liter in Betrieb genommen und arbeitet jetzt mit einer Kapazität von über 530 Millionen Liter. Im Dezember 2019 erwarb GLE zwei weitere Bioethanol-Produktionsanlagen in Aberdeen und Huron, South Dakota. Die Anlage in Aberdeen produziert derzeit etwa 190 Millionen Liter, während es in Huron circa 150 Millionen Liter Bioethanol sind. Insgesamt kaufen die Bioethanolanlagen von GLE mehr als 125 Millionen Scheffel Mais pro Jahr und produzieren mehr als 1,363 Milliarden Liter Ethanol, 918.000 Tonnen Futtermittelprodukte/Destillierschrot und 51.000 Tonnen Maisöl pro Jahr.
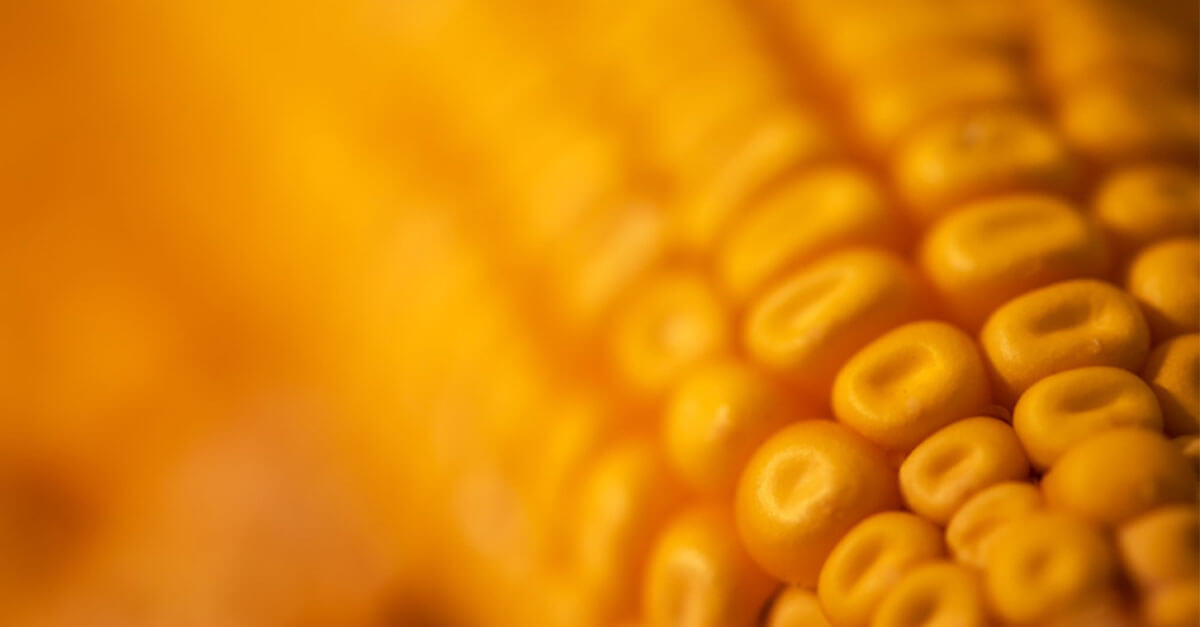
Maisöl als wertvolles Nebenprodukt der Bioethanolherstellung
Bioethanol entwickelt sich zunehmend als nachhaltige Alternative zu fossilem Benzin. Verschiedene nachwachsende Rohstoffe, wie beispielsweise Zuckerrüben, Mais oder Kartoffeln sind die Grundlage für die Bioethanolproduktion. Als die wichtigste Rohstoffquelle dient dabei Mais. Klassische Bioethanolanlagen produzieren Ethanol, Feststoffe und einen Restsirup, der durch Verdampfen und Trocknen der Dünnschlempe entsteht. Immer mehr Anlagenbetreiber nutzen eine weitere innovative Möglichkeit der Rohstoffgewinnung: Hierbei wird mit einem Tricanter® Maisöl als weiteres Wertprodukt aus der Dünnschlempe gewonnen. Das Maisöl kann anschließend als Futtermittelzusatz oder für die Herstellung von Biodiesel verwendet werden.
Aufbau und Funktionsweise eines Tricanter® sind ähnlich wie bei einem Dekanter (2-Phasen-Trennung). Der entscheidende Unterschied dieser beiden Maschinen liegt in der Ableitung der Flüssigkeit. Bei einem Tricanter® werden drei Phasen abgetrennt, der Feststoff und zwei Flüssigphasen: Eine „schwere“ Flüssigphase (höhere Dichte und abgeleitet unter Druck) sowie eine „leichte“ Flüssigphase (geringere Dichte und drucklos abgeleitet). Nach diesem Prinzip werden die Öle aus der Dünnschlempe separiert und ein zusätzlicher Rohstoff gewonnen. Dank verstellbarer Schälscheibe kann der Tricanter® sehr flexibel auf veränderte Produktbedingungen angepasst werden und gewährleistet dadurch immer ein optimales Trennergebnis und höchste Produktqualität. Eine erhöhte Ölausbeute sorgt für eine schnelle Amortisation der Investition.
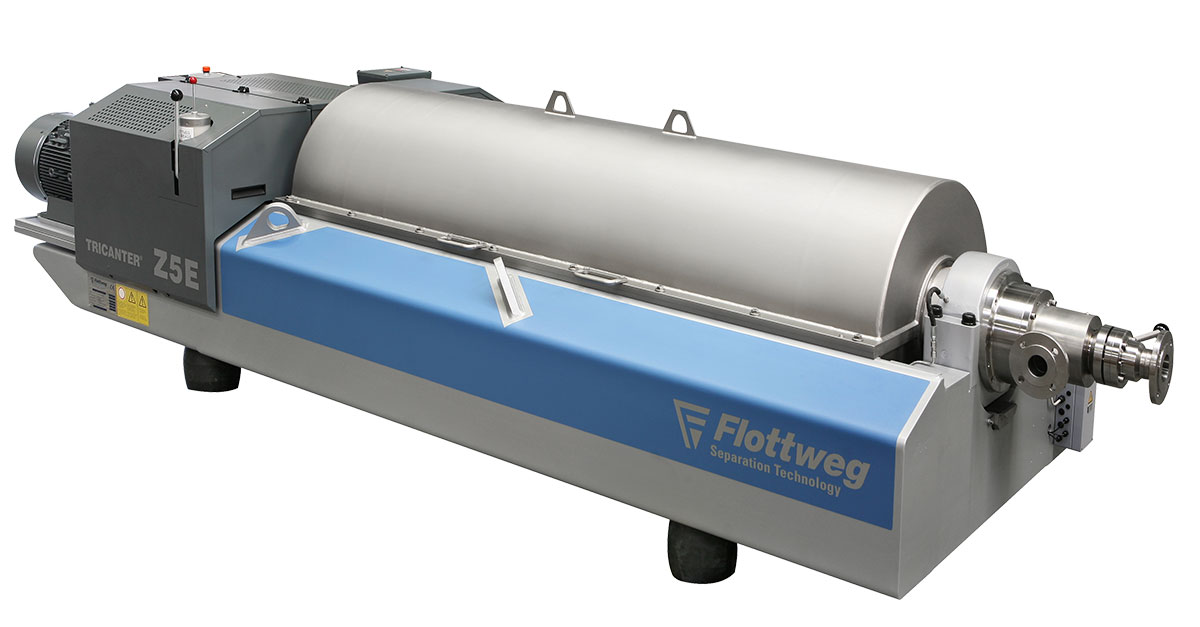
Geringe Ölausbeute und zu kleine Maschine: Die Herausforderungen bei Glacial Lakes Energy LLC
GLE setzte in Aberdeen bisher einen Teller-Separator für die Ölrückgewinnung und ‑abscheidung ein. Da die Maschine zu klein war, eine schlechte Rückgewinnungsrate hatte und sowie eine geringe Ölausbeute lieferte, entschied man sich eine Alternative zu suchen. Dabei war Pat Horgan von Beginn an überzeugt, dass die Produktion mit einer aufgerüsteten Anlage gesteigert werden könnte. Nach reichlicher Recherche waren schließlich zwei Trennlösungen im Rennen: „Für uns stellte sich schließlich die Frage entweder einen weiteren Separator zu installieren oder auf eine andere Technologie, wie die Dreiphasentrennung umzusteigen“, erklärt Pat Horgan. „Aus Perspektive der reinen Ölabscheidung sind beide Technologien gut. Für die Rückgewinnung von Maisöl aus der Bioethanolproduktion tendierten wir jedoch stark zur Dreiphasentrennung. Daher entschieden wir uns für einen Flottweg Tricanter®.“ Die ersten Ergebnisse mit dem Tricanter® sorgten dann für vollste Zufriedenheit in Aberdeen und bei Horgan: „Nachdem wir den Tricanter® eingesetzt hatten, zeigte sich eine deutliche Erhöhung der Kapazität.“
Anfang 2021 befand sich die Anlage in Mina in einer ähnlichen Lage wie zu Beginn in Aberdeen: Die Separatoren produzierten kein qualitativ hochwertiges Öl und hatten eine geringe Ölausbeute. „Wir standen wieder vor der Entscheidung, das System aufzurüsten oder stattdessen wieder eine Dreiphasentrennungeinzusetzen“, erklärt der Betriebsleiter. „Wir entschieden uns schließlich erneut für zwei Tricanter® mit einem tollen Ergebnis: Nach der Installation der Tricanter® konnten wir die Ölausbeute verdoppeln.“ Da die beiden Separatoren noch voll funktionsfähig waren, beschloss Hogan, eine Maschine in Mina als Reserve für die wöchentlichen Tricanter® CIP-Verfahren zu belassen.
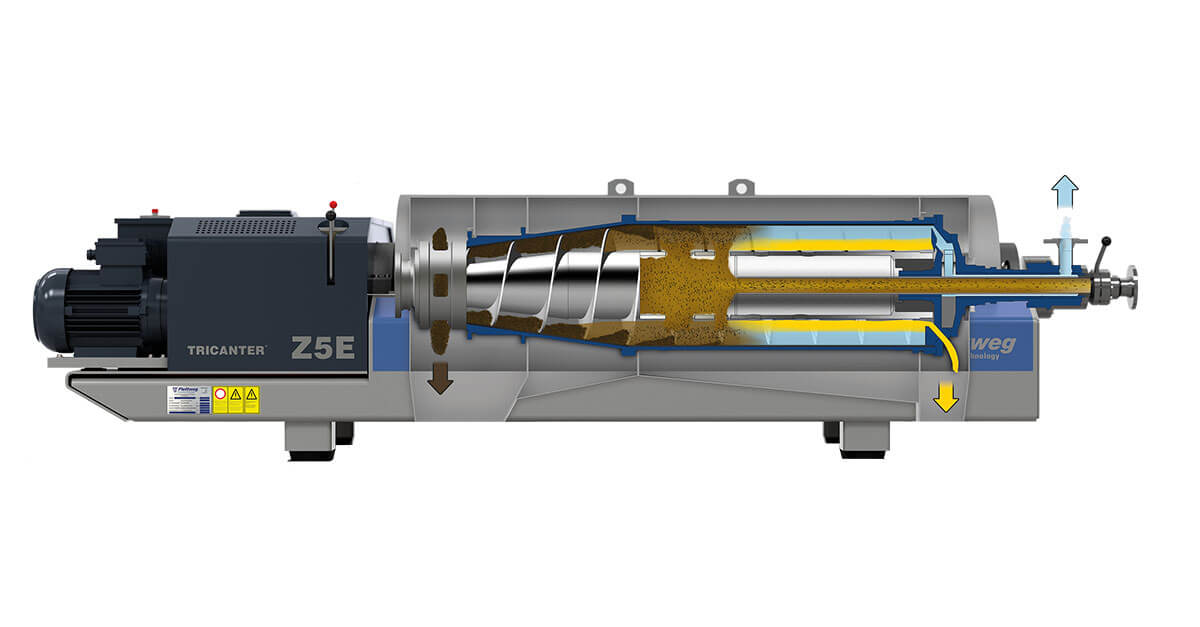
Die Lösung der Probleme: Der Flottweg Tricanter®
Obwohl der Tricanter® in der Anschaffung etwas teurer war als der Separator, gab es aus Sicht des Geschäftsführers Hogan mehrere entscheidende Gründe, die für den Tricanter® sprachen. Besonders ausschlaggebend war für Hogan die Handhabung der Maschine: „Der Hauptgrund, warum ich mich schließlich für den Tricanter® entschieden habe, ist, dass er deutlich einfacher zu bedienen ist", erläutert Hogan. „Zur einfachen Bedienung kommt hinzu, dass er viel störungsunanfälliger als die alten Separatoren ist. Der Wartungsaufwand für einen Flottweg Tricanter® ist bei Weitem geringer als der für einen Separator. Bei entsprechender Pflege der Maschinen reicht eine jährliche Wartung völlig aus. Bei den Separatoren dagegen sind zusätzlich zur jährlichen Großwartung vierteljährliche Wartungen erforderlich.“ Auch bei der Reinigung bemerkte Hogan, dass ein Tricanter® im Vergleich zu den Separatoren, die zusätzlich zu den wöchentlichen Reinigungen täglich mehrere Wasserspülungen benötigen, wesentlich einfacher in der Handhabung ist.
Aus Hogans Blickwinkel rechtfertigen diese wesentlichen Vorteile die Anschaffungskosten für den Tricanter®: „Wir haben einige wirklich gute Leute, die sich um die Separatoren in unseren Anlagen kümmern. Aufgrund ihrer Erfahrung lassen sie den Umgang mit Separatoren und die damit verbundene Arbeit einfach aussehen. Aber ich weiß auch, dass diese Anlagen eine Menge Kopfschmerzen bereiten können, wenn man ihnen nicht 100 Prozent Aufmerksamkeit schenkt und nicht alle Prozesse reibungslos ablaufen“, verdeutlicht Hogan. „Der Tricanter® macht es uns an dieser Stelle viel leichter und ist einfach viel bedienungsfreundlicher.“
Auch in Zukunft würde Hogan wieder Flottwegs Trenntechnologie und insbesondere den Tricanter® wählen: „Ich würde mich wieder für Drei-Phasen-Dekanter von Flottweg entscheiden, denn sie laufen vom ersten Tag an. Man installiert sie, kümmert sich entsprechend um sie und dann laufen die Maschinen einfach. Das ist für mich das Wichtigste.“

Sie haben Interesse an Flottweg Zentrifugen?
Sprechen Sie uns an oder schreiben Sie uns.