07.11.2022
Podwojenie uzysku — Flottweg Tricanter® w produkcji bioetanolu w zakładzie Glacial Lakes Energy LLC
Glacial Lakes Energy LLC posiada cztery zakłady produkcji bioetanolu w południowo-wschodniej Dakocie w północno-zachodniej części USA. Wyróżnia się też ponad 20-letnim doświadczeniem w produkcji bioetanolu. Produktem ubocznym produkcji bioetanolu jest olej kukurydziany. Ta amerykańska firma odsprzedaje go jako cenny surowiec. Aby poprawić uzysk i jakość oleju kukurydzianego, firma Glacial Lakes Energy LLC zdecydowała się na zastosowanie urządzenia Tricanter® marki Flottweg w swoich dwóch zakładach. Dzięki nowej technologii separacji możliwe było osiągnięcie wyższego uzysku oraz produkcja oleju o najwyższej jakości. Jednocześnie czasy eksploatacji zostały wydłużone przy mniejszych nakładach na konserwację.
Glacial Lakes Energy dysponuje czterema zakładami produkcji bioetanolu w południowej Dakocie: Aberdeen, Huron, Mina i Watertown. Wszystkie cztery obiekty są zarządzane przez dyrektora zarządzającego, Pata Hogana, i są położone od siebie w promieniu dwóch godzin. Każdy zakład ma kierownika operacyjnego, produkcji i konserwacji odpowiedzialnego za konserwację i eksploatację poszczególnych obiektów.
Zakład w GLE Watertown rozpoczął swoją działalność w sierpniu 2002 roku. Początkowo osiągał nominalną pojemność 40 milionów galonów rocznie (MMgy), co odpowiada około 150 milionom litrów rocznie. W 2007 roku zakład ten został rozbudowany i obecnie produkuje ponad 130 mm bioetanolu. Zakład GLE Mina został oddany do użytku w czerwcu 2008 r. Początkowa produkcja wynosiła około 110 Mmgy. Obecna wydajność to ponad 140 MMgy. W grudniu 2019 r. firma GLE przejęła dwa dodatkowe zakłady produkcji bioetanolu w Aberdeen i Huron w południowej Dakocie. Obecnie zakład w Aberdeen produkuje około 50 MMgy, a Huron — 40 MMgy bioetanolu. Zakłady produkujące bioetanol należące do GLE kupują rocznie w sumie ponad 125 milionów buszli kukurydzy i wytwarzają rocznie ponad 360 MMgy etanolu, 918 000 ton pasz zwierzęcych/mączki destylacyjnej oraz 51 000 ton oleju kukurydzianego.
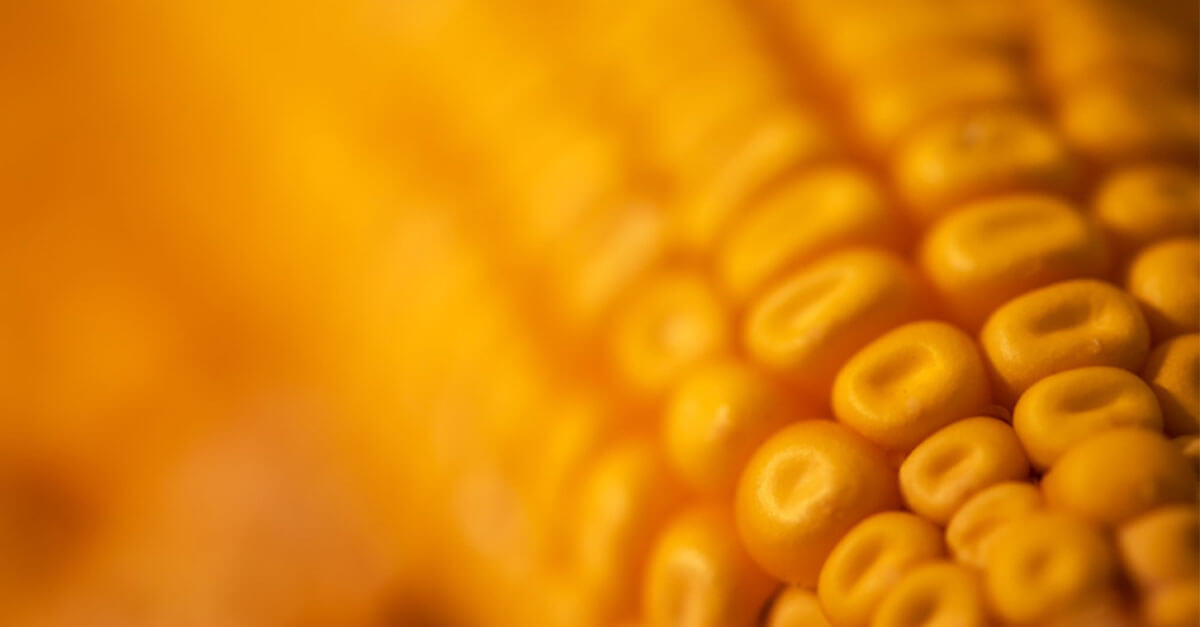
Olej kukurydziany jako cenny produkt uboczny powstały podczas produkcji bioetanolu
Bioetanol szybko staje się zrównoważoną alternatywą dla paliw kopalnych. Podstawą produkcji bioetanolu są różne surowce odnawialne, takie jak buraki cukrowe, kukurydza czy ziemniaki. Kukurydza jest przy tym najważniejszym źródłem surowców. Tradycyjne zakłady produkujące bioetanol wytwarzają etanol, ciała stałe i syrop resztkowy, które powstają w wyniku parowania i suszenia rzadkiego wywaru gorzelnianego. Coraz większa liczba operatorów zakładu korzysta z innej innowacyjnej metody ekstrakcji surowców, która wykorzystuje urządzenie Tricanter® w celu uzyskania kolejnego cennego produktu z rzadkiego wywaru gorzelnianego: oleju kukurydzianego! Olej kukurydziany może być następnie stosowany jako dodatek do paszy lub do produkcji biodiesla.
Budowa i zasada działania urządzenia Tricanter® przypominają budowę i zasadę działania dekantera (oddzielanie dwufazowe). Decydującą różnicą pomiędzy tymi dwoma maszynami jest sposób odprowadzania cieczy. Urządzenie Tricanter® ma trzy fazy oddzielania — materiał stały w jednej i materiał ciekły w dwóch fazach: faza ciekła „ciężka” (większa gęstość i odprowadzanie pod ciśnieniem) oraz faza ciekła „lekka” (mniejsza gęstość i odprowadzanie bez ciśnienia). Na podstawie tej zasady oleje są oddzielane od rzadkiego wywaru gorzelnianego i uzyskiwany jest dodatkowy surowiec. Dzięki przestawnej tarczy skórującej (cedzidle) można bardzo łatwo dostosować urządzenie Tricanter ® do zmieniających się warunków produkcji, aby zagwarantować optymalny wynik oddzielania i najwyższą jakość produktu. Zwiększony uzysk oleju zapewnia szybki zwrot z inwestycji.
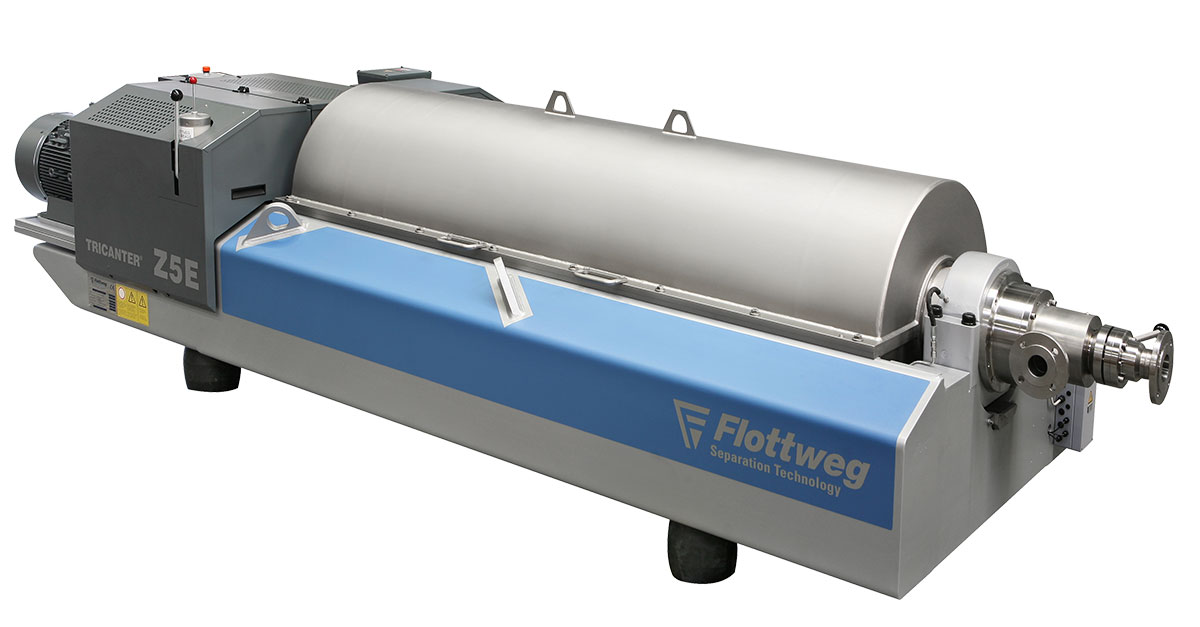
Niski uzysk oleju i nieodpowiednia wielkość maszyny: Wyzwania w Glacial Lakes Energy LLC
Wcześniej w zakładzie GLE w Aberdeen stosowano separator talerzowy do odzyskiwania i oddzielania oleju. Jednak ponieważ maszyna była zbyt mała, odnotowano niski stopień odzysku oraz niski uzysk oleju. Postanowiono więc znaleźć inne rozwiązanie. Pat Hogan od samego początku był przekonany, że produkcję można zwiększyć, modernizując zakład. Po szeroko zakrojonych badaniach do fazy końcowej przeszły dwa rozwiązania do oddzielania: „Ostatecznie chodziło nam o to, aby zainstalować inny separator lub przejść na inną technologię, taką jak oddzielanie trzech faz”, wyjaśnia Pat Hogan. „Obie technologie są dobre, jeśli chodzi o oddzielanie oleju. Jednak jeśli chodzi o odzyskiwanie oleju kukurydzianego podczas produkcji bioetanolu, naszym faworytem było oddzielanie trzech faz. Dlatego zdecydowaliśmy się na urządzenie Tricanter® firmy Flottweg”. Pierwsze wyniki uzyskane za pomocą urządzenia Tricanter® były w pełni satysfakcjonujące dla pracowników Aberdeen i Hogana: „Po zastosowaniu urządzeniaTricanter® odnotowaliśmy znaczny wzrost wydajności”.
Na początku 2021 roku zakład w Mina znalazł się w sytuacji podobnej jak niegdyś zakład w Aberdeen: Separatory nie zapewniały oleju wysokiej jakości a uzysk oleju był niski. „Po raz kolejny stanęliśmy przed decyzją o modernizacji systemu lub zastosowaniu oddzielania trzech faz”,wyjaśnia kierownik operacyjny. „Wreszcie znów zdecydowaliśmy się na dwa urządzenia Tricanter®i osiągnęliśmy świetny wynik. Po zainstalowaniu urządzenia Tricanter® udało nam się podwoić uzysk oleju”. Ponieważ oba separatory były nadal w pełni sprawne, Hogan zdecydował się pozostawić maszynę w Mina jako zapasowe urządzenie do cotygodniowych procedur CIP Tricanter® .
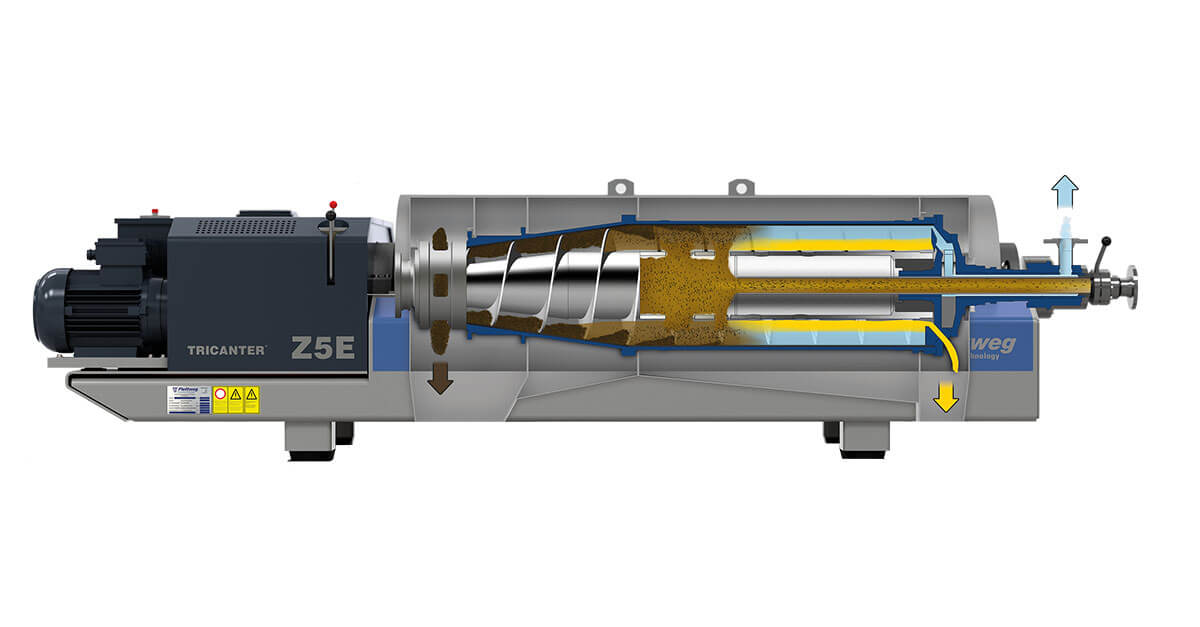
Rozwiązywanie problemów: Wirówka Tricanter® marki Flottweg
Chociaż urządzenie Tricanter® było nieco droższe niż separator, dyrektor zarządzający Pat Hogan wierzył, że istnieje kilka kluczowych zalet, które przemawiają za urządzeniem Tricanter®. Sposób obsługi maszyny był dla Hogana bardzo ważny: „Głównym powodem, dla którego ostatecznie zdecydowałem się na urządzenie Tricanter® jest fakt, że jest ono znacznie łatwiejsze w użyciu”, wyjaśnia Hogan. „Oprócz łatwości obsługi, jest też znacznie mniej podatne na usterki niż stare separatory. Koszt konserwacji wirówki Flottweg Tricanter® jest zatem znacznie niższy niż koszt konserwacji separatora. Gdy maszyny są odpowiednio konserwowane, wystarczy robić to raz na rok. Separatory natomiast wymagają kwartalnej konserwacji oprócz szeroko zakrojonych prac konserwacyjnych co roku”. Jeśli chodzi o łatwość czyszczenia, Hogan zauważył również, że urządzenie Tricanter® jest o wiele łatwiejsze w obsłudze niż separatory, które muszą być płukane wodą kilka razy dziennie, a do tego czyszczone raz na tydzień.
Z punktu widzenia Hogana, te główne zalety uzasadniają koszt zakupu Tricanter® : „Mamy naprawdę dobrych techników, którzy dbają o separatory w naszych zakładach. Dzięki ich doświadczeniu obsługa separatorów i związane z tym prace wydają się proste. Wiem również, że w zakładach może wystąpić wiele problemów. Jeśli nie poświęci się maszynom 100% uwagi, nie wszystkie procesy będą przebiegać płynnie” — wyjaśnia Hogan. „Pod tym względem urządzenie Tricanter® znacznie ułatwia pracę i jest po prostu bardziej przyjazne dla użytkownika”.
W przyszłości Hogan zamierza nadal stawiać na technologię oddzielania marki Flottweg, a w szczególności na urządzenia Tricanter®: „Ponownie zdecydowałbym się na trójfazowe dekantery marki Flottweg, ponieważ sprawnie pracują one od samego początku. Instalujesz je, odpowiednio o nie dbasz, a maszyny pracują sprawnie. To dla mnie najważniejsze”.
Autor:
Bill Griffiths, technologia oddzielania Flottweg
Kierownik sprzedaży — Jadalne tłuszcze i oleje
bgriffiths@flottweg.net

Czy interesują Cię wirówki marki Flottweg?
Porozmawiaj z nami lub napisz do nas!