2022-07-20
10 facts about Flottweg’s new nozzle separator
Flottweg has now launched a sustainable and powerful separation unit: the nozzle separator. The following 10 facts provide an overview of the features and functions of the Flottweg newcomer:
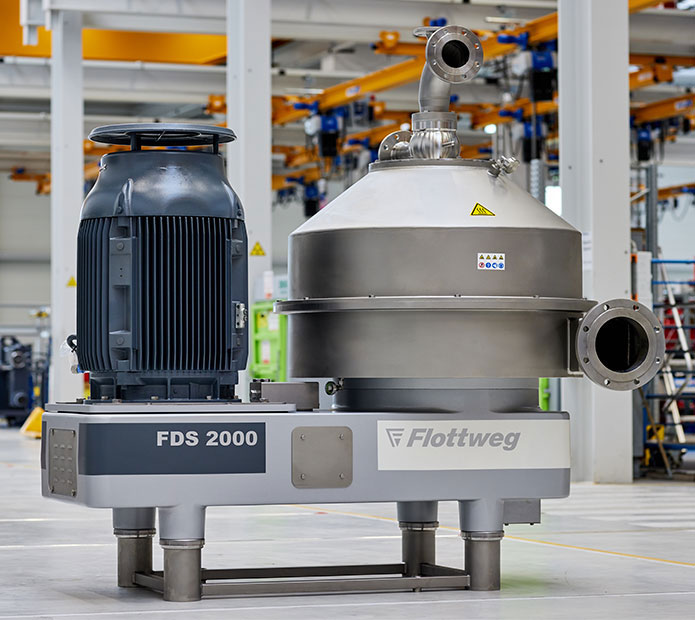
1. The nozzle separator can be used in the food and starch industry, as well as in biotechnology or the chemical industry.
In the starch industry and in many other areas of application, maximum clarification or separation is required with consistently high quantities of solids. Therefore, the nozzle separator can be used for separation tasks in the food industry, especially for wet starch or ethanol production. However, the nozzle separator's range of applications is constantly being tested; Flottweg is continuously conducting exciting and extremely interesting trials.
2. Flottweg worked together with the customer to develop the nozzle separator.
As a separation technology specialist, Flottweg always strives to offer its customers the best solutions for their respective processes. The driving force behind the development of the nozzle separator originated from various customers' inquiries. This impetus, combined with decades of experience with the AC separator series finally led to the decision to expand the product portfolio to include a high-performance nozzle separator. Thus, in the design and construction of the nozzle separator, special attention was paid to a material-saving and efficiency-optimized design. This conserves resources and also lowers operating costs, thereby meeting customer requirements at the same time.
3. Solids and liquids are clarified or separated by the nozzle separator with a high degree of efficiency.
The nozzle separators also have the largest possible clarification area and can process large quantities of solids thanks to the continuous solids discharge. Customers receive consistently pure solids in the lower outlet. At the same time, the upper flow outlet is optimally cleaned and is ready for subsequent separation processes. Flottweg provides two basic versions: The clarifier / 2-phase nozzle separator and the concentrator / 3-phase nozzle separator.
4. The 2-phase nozzle separator is a clarifier.
2-phase nozzle separators serve to separate solids from liquids, thus making highly efficient clarification possible.Large solid particles are separated directly in the centrifugal field of the 2-phase nozzle separator. Finer solids are separated when flowing through the disc stack. The solid particles collect in the bowl's outer solids chambers. From there, they are continuously discharged via the nozzles. The clarified liquid flows from the disk stack and is discharged under pressure via an impeller.
5. The 3-phase nozzle separator is a concentrator.
In addition to separating solids from liquids, 3-phase nozzle separators are used to fractionate different particle sizes. With 3-phase nozzle separators, larger solid particles are separated as they flow through the disc stack and are directed to the edge of the bowl as a result of the high centrifugal force. There, they collect in the bowl's outer solids chambers and are continuously discharged through the nozzles.
The remaining product flow is then directed to a middle and an upper outlet. Solids with a smaller particle size form the middle flow, which is discharged under pressure. The remaining liquid flows through the disk stack, thus creating a nearly clear upper flow. This is also discharged under pressure via an additional impeller.
6. The bowl is the heart of the separator.
Thanks to the highly innovative design of the bowl, the nozzle separator combines a wide range of positive features. Among these positive features, we should highlight the particularly quiet running of our system and the maximum energy savings offered due to the controlled discharge from the lower outlet. The rotation of the bowl is assisted by the discharge from the lower outlet, thus saving drive energy. In addition, the complete bowl is a compact unit that can be easily assembled and disassembled, thus facilitating maintenance.
7. The new product is designed for perfect hygiene.
The nozzle separator meets all the requirements of the applicable centrifuge standard and is constructed according to "Hygienic Design" principles. The innovative solids chambers in the separator bowl ensure that the concentrate is discharged from the bowl without deposits and that no deposits remain when the machine is shut down. All components of the separator that come into contact with the product are made of high-quality stainless steel. The hygienic design of the Flottweg nozzle separator avoids dead zones and thus makes cleaning the centrifuge easy. In the food and biotechnology industries, all components that come into contact with the product are CIP-capable (Clean-in-Place) and can be easily integrated into existing cleaning processes.
8. The nozzle separator is quick and easy to maintain.
Fast and predictable maintenance makes a decisive contribution to smooth operation. The innovative design of the separator bowl prevents wear. The arrangement of the nozzles creates a natural wear protection of solid material in the bowl. The nozzles of the Flottweg Nozzle Separator are equipped with carbide wear protection for maximum service life. These nozzles can be replaced quickly and easily via a maintenance opening in the housing. The nozzle separator's compact spindle drive is also optimized for minimum downtime during maintenance. This can be removed quickly and easily with little effort. The separator drive belt can be easily retightened or quickly replaced through a maintenance opening. High-quality materials 'Made in Germany' ensure that maintenance intervals are extended. For our customers, this means higher availability and lower costs.
9. Sustainability was a decisive factor in the development of the nozzle separator.
From its conception to the implementation of the nozzle separator, the topic of sustainability remained at the forefront. The saving of resources and materials together with the efficient design of the nozzle separator allows the product innovation to be energy-efficient yet powerful: The nozzle separator provides high throughput and excellent separation results while consuming very little energy. These are influential criteria that also have a particular impact on operating costs and enable costs to be reduced. This shows that the topic of sustainability brings many advantages when implemented consistently, and therefore will continue to drive development at Flottweg in the future.
10. The compact spindle drive makes the nozzle separator particularly energy-efficient and easy to maintain.
The compact spindle drive is a special feature of the nozzle separator. The compact spindle is mounted in rubber elements and ensures low-vibration and well-damped operation. The power is transmitted by a robust belt drive. The drive motor is controlled by a frequency converter, which makes it possible to achieve an infinitely variable bowl speed together with smooth acceleration and regenerative braking. The operating speed can be checked via the control system display. The measured value is determined via frequency converter and pulse generator (initiator).