2022-10-26
Energy-saving, maintenance-optimized and powerful – Flottweg’s new nozzle separator
The nozzle separator is mainly used when continuous separation of large quantities of solids from liquids is required together with maximum clarification or separation. The nozzle separator is therefore particularly suitable for use in the starch industry as well as in ethanol production. Flottweg from Lower Bavaria is now presenting its nozzle separator for the first time and has brought a sustainable and high-performance separation unit to the market using the experience and knowledge gained from more than 60 years as a separation technology specialist.
According to Matthias Gaube, Product Manager at Flottweg, customer inquiries played a key part in the development of a nozzle separator: "Together with our customers, we developed the nozzle separator and focused on one goal: Developing a nozzle separator that is perfectly tailored to customer needs. The result is an innovative, energy-optimized, low-wear design." The planning and realization of the nozzle separator took just one year, which meant that we were able to react quickly to the customer's requirements and wishes.
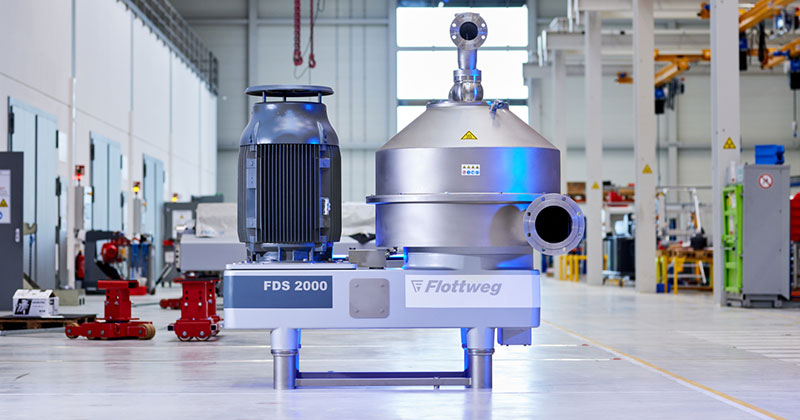
Functionality of the nozzle separator
Flottweg nozzle separators (2- and 3-phase nozzle separators) are used for the continuous separation of solids from liquids and ensure highly efficient clarification or separation. The product to be clarified or separated flows via a stationary inlet pipe into the inside of the bowl and is gently accelerated to operating speed by the distributor. Large solid particles are separated directly in the centrifugal field of the 2-phase nozzle separator. Finer solids are separated when they flow through the disk stack. The solid particles collect in the bowl's outer solids chambers. From there, they are continuously discharged via the nozzles. The clarified liquid flows from the disk stack and is discharged under pressure via an impeller.
Larger solid particles are separated in the 3-phase nozzle separator as they flow through the disc stack and are then directed to the edge of the bowl by the high centrifugal force. There, they collect in the bowl's outer solids chambers and are continuously discharged through the nozzles. The remaining product stream divides into a middle and upper flow outlet. Solids with a smaller particle size form the middle flow, which is discharged under pressure. The remaining liquid flows through the disk stack, thus creating a nearly clear upper flow. This is also discharged under pressure via an additional impeller.
The nozzle separators also have the largest possible clarification area and can process large quantities of solids thanks to continuous solids discharge. Customers receive consistently pure solids in the lower outlet. At the same time, the upper flow outlet is optimally cleaned and is ready for subsequent separation processes. Depending on the separation task, the throughput of the nozzle separator can be varied from 40 m³/h to 160 m³/h.
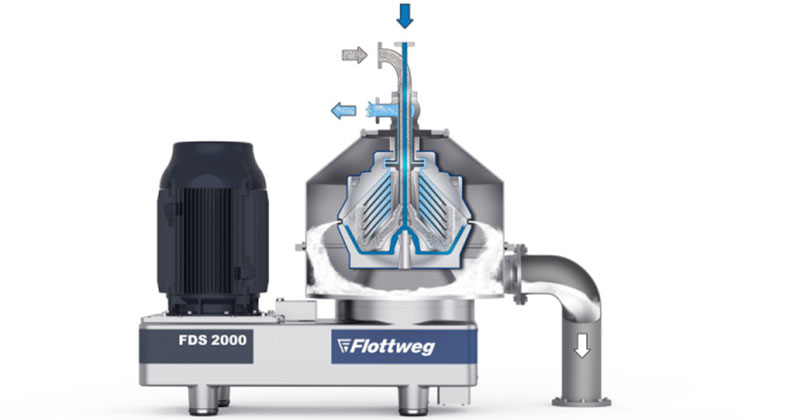
Starch for use in the food industry
Starch can be used in many processes – in the food industry as a binding or thickening agent in the production of baked goods, in soups and sauces, in the paper and corrugated cardboard industry, and in the chemical, pharmaceutical, and cosmetics industries. Optimum clarification or separation combined with high solids content is required in the starch industry. Flottweg’s nozzle separators are primarily used here. The Flottweg nozzle separator's spectrum of use covers various starch applications. In addition to the production of wheat and potato starch, the nozzle separator can also be used in the corn or tapioca starch production process.
Outstanding results are achieved with the Flottweg nozzle separator, especially in conjunction with the washing or recirculation device. This device makes it possible to feed process/wash water or an already concentrated product directly into the solids chambers upstream of the nozzle outlet, at operating speed, to reliably compensate for product fluctuations. In addition, the washing device separates fiber fragments and dissolved substances from the starch fraction with greater efficiency. The optional 3-phase version of the Flottweg nozzle separator offers a further benefit in the production of wet starch. It can produce a near-clear upper flow that can be returned directly to the process as process water, removing the need for additional fresh water and further steps.
Focus on sustainability
During the development of the nozzle separator, the focus was primarily on sustainability: The saving of resources and materials together with the efficient design of the nozzle separator allows the product innovation to be energy-efficient yet powerful: The nozzle separator provides high throughput and excellent separation results while consuming very little energy. Influential criteria that also have a particular impact on operating costs and enable costs to be reduced.
Key to these energy savings and efficiency is the heart of the machine, the bowl. The revolutionary design of our bowl saves drive energy. In addition, the nozzle separator bowl is significantly lighter than a conventional bowl and therefore requires less drive energy. The separator bowl design ensures reliable and low-vibration operation. Solids chambers integrated into the bowl prevent uncontrolled sedimentation and can prevent vibrations. The concentrate can be conveyed out of the bowl via the solids chambers without leaving deposits. The size of the nozzles' outlets is optimally adapted to the respective process and to the product to be processed.
Simple and fast maintenance
Already in the design phase, great importance was attached to another feature of the nozzle separator: The design of the separator is optimized for ease of maintenance. "For us, this means not only optimal maintenance but also the general avoidance of parts requiring maintenance or are subject to wear," explains Matthias Gaube. "Thus, our contactless sealing system allowed us to significantly reduce potential wear already in the design stage." But even maintenance work that must still be undertaken has been optimized to the greatest possible degree thanks to the innovative and low-wear design of the separator bowl. The arrangement of the nozzles creates a natural wear protection of solid material in the bowl. The nozzles of the Flottweg Nozzle Separator are equipped with carbide wear protection for maximum service life. These nozzles can be replaced quickly and easily via a maintenance opening in the housing. The compact spindle drive also deserves special mention: Thanks to the clever design of the nozzle separator, the spindle can be released and replaced quickly by removing just four screws, if necessary.
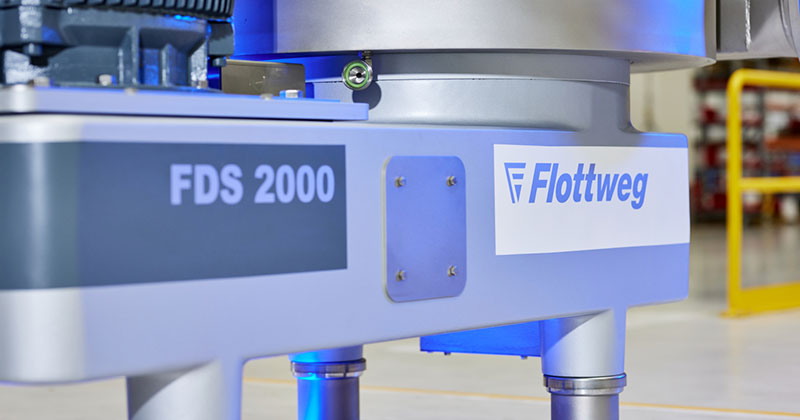
Designed for perfect hygiene
Whether for food, biotechnology or chemistry, the nozzle separator is ideally equipped to meet the hygienic standards in highly regulated industrial sectors. The innovative solids chambers in the separator bowl ensure that the concentrate is discharged from the bowl without deposits and that no deposits remain when the machine is shut down. All components of the separator that come into contact with the product are made of high-quality stainless steel. The hygienic design of the Flottweg nozzle separator avoids dead zones and thus makes cleaning the centrifuge easy. In the food and biotechnology industries, all components that come into contact with the product are CIP-capable (Clean-in-Place) and can be easily integrated into existing cleaning processes.
Ready for use
The first tests with the nozzle separator have already provided clear results: "Since this is a new separator, we were expecting to have to make some changes during the first tests," explains the product manager, "but the first tests proved us wrong. Almost from the very first moment, we were able to integrate our separation unit into our test partner's process. We were delighted to see that our nozzle separator far surpasses the efficiency targets we have set ourselves."
Matthias Gaube is also very optimistic about the nozzle separator's field of application: "We have already been able to comprehensively and successfully test our nozzle separator in the areas of wet starch and ethanol production. However, we are in a constant process of expanding our range of applications and are continuously conducting exciting and highly interesting trials."