2022-01-20
Sand treatment with spin cycle
In sand preparation, Reithelshöfer GmbH saves over 90 percent process water by using a decanter centrifuge and at the same time reduces investment and operating costs.
If you were to ask people in the street today which raw materials they consider to be the most important, hardly anyone would mention the word "sand". Sand is worldwide one of the most basic raw materials. Gigantic quantities are needed every year to build houses, airports, roads and much more, for example. And since sand is not just sand and cannot be removed from the ground in the desired quality, companies such as Sandvertriebs- und Verwertungsgesellschaft mbH & Co. KG of the Reithelshöfer Group near Nuremberg process these resources. Tonnes of gravel and sand are extracted every day, and of course it is also a question of economical and resource-saving production. Efficient use of water plays a decisive role in this. The Reithelshöfer company has gained an enormous competitive advantage since they began using a Flottweg decanter centrifuge for washing water treatment: The new technology has reduced the fresh water requirement from 350 cubic metres per hour to just 20 cubic metres per hour.
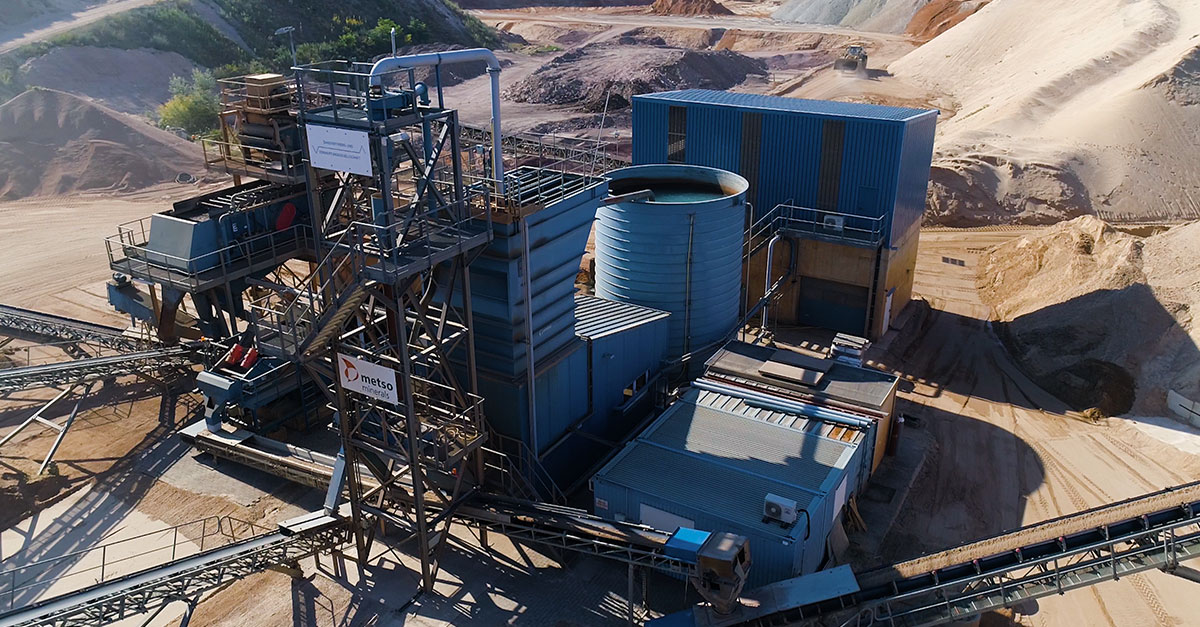
Separation in stages
Huge amounts of water are required to extract sand. Finally, the extracted material must be separated into its components, including gravel, sand, clay and coal, to name just a few. With sieves and the use of a lot of water, soluble parts are flushed out and the valuable material is separated into different grain sizes via ever finer sieves - until exactly the sand and gravel grain size is obtained as required for different applications. One of the major challenges in the treatment process is the amount of water required. To minimize the amount of fresh water that has to be continuously supplied, the wash water is separated from the washed-out particles and reused. Consequently: The more precious water that can be separated and purified from the residual mass, the more efficient the entire manufacturing process is - from an economic as well as an energetic and ecological point of view.
Traditional sludge dewatering reaches its limits
Traditionally, washing water is purified in two steps, which are still used in many companies today: First, the coarse particles are separated from the water via the sedimentation process, for example in an oblique clarifier. A vacuum band filter is then often used, which separates a further proportion of the water from the sludge with the addition of a flocculant. In view of today's technological standards and ever-increasing production volumes, this type of sludge dewatering is no longer efficient enough.
To make matters worse, new regulations are being constantly introduced and rising costs are forcing producers to keep tailings piles as small as possible and to reduce the amount of fresh water to a minimum.
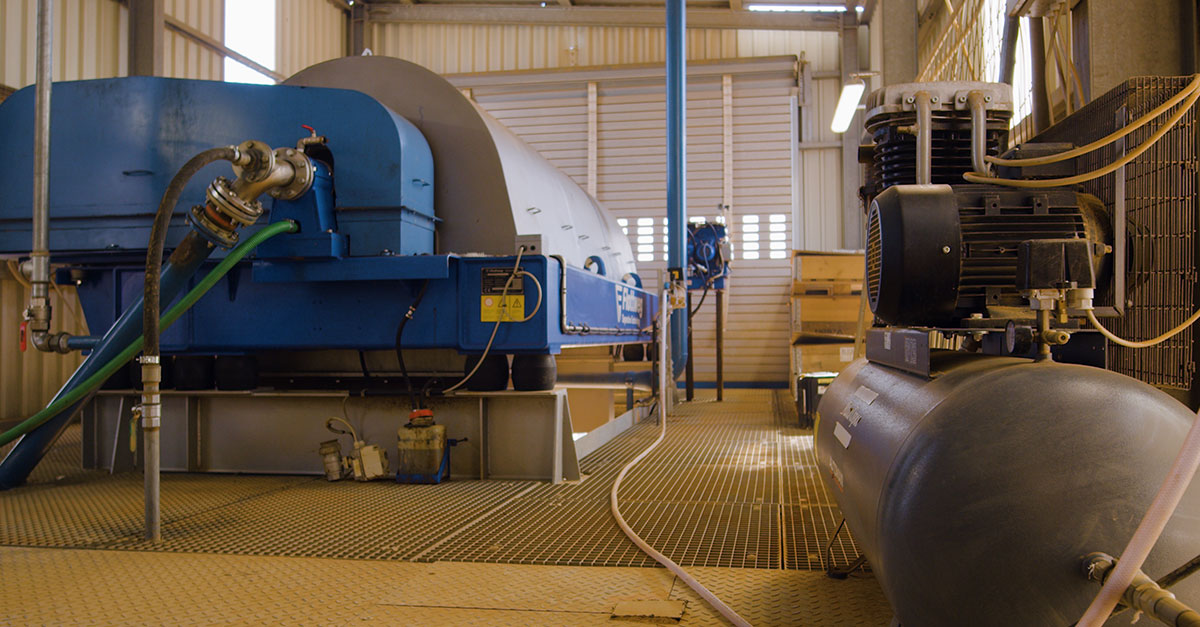
Adopting innovative procedures
Those responsible at the sand processing company Reithelshöfer GmbH near Nuremberg were also concerned about the recovery of water from sand processing and about the costs of large spoil heaps - for which it is now almost impossible to obtain permits - and about cost-effectiveness. The company has always been innovative in the way it tackles challenges, and several years ago its technicians were convinced that special attention should be paid to the treatment and purification of wash water. The people at Reithelshöfer then made a decision that was rather unusual in the industry, but quite innovative. In order to achieve a much more efficient treatment of the sand washing water and to avoid losing large quantities of water with wet sludge on the ever-growing spoil heaps, Reithelshöfer opted for a process that has long been standard in other industrial sectors: decanter centrifuge technology.
Flottweg's decanter centrifuge was chosen in 2003. This company from Vilsbiburg in Bavaria is a pioneer in centrifuge technology and offers machines for separating liquids from solids for almost every conceivable application. Reithelshöfer uses the Flottweg Z92 model, which enables true parallel operation with its high separation capacity of up to 15 metric tons per hour. The advantage: During sand preparation, the centrifuge separates so much clean water from the used wash water that no run-on for washing water cleaning is required afterwards. The decanter centrifuge at Reithelshöfer is adjusted so that particles smaller than 25 µm are also separated from the water.
Flottweg's centrifuge also scores points with further decisive advantages over other technologies. In contrast to chamber filter presses or belt filter presses, several of which would be needed in parallel to achieve approximately similar results, a single centrifuge is sufficient at Reithelshöfer. As a result, much less steelwork was required for the structure and the overall outlay in terms of procurement and installation was significantly lower. At the same time, the costs for maintenance and operation of just one machine are significantly lower. Since the decanter can dewater the sludge to up to 55 percent dry solids in just one pass, intermediate storage of the thickened sludge in a holding tank is also no longer necessary. Due to the high degree of dewatering, the residual sludge can be transported directly from a bunker located under the machine with the wheeled loader.
The fact that centrifuge technology is a worthwhile investment is particularly noticeable in fresh water consumption, both economically and environmentally: Due to the significantly higher separation compared to other processes, much more water is returned to the production process. "With traditional separation methods, a fresh water supply of no less than 350 cubic metres per hour was required. With the use of the Flottweg centrifuge, recovery is significantly more efficient and we only need 20 cubic metres of fresh water", explains Stefan Köhn, Managing Director of M. Reithelshöfer GmbH.
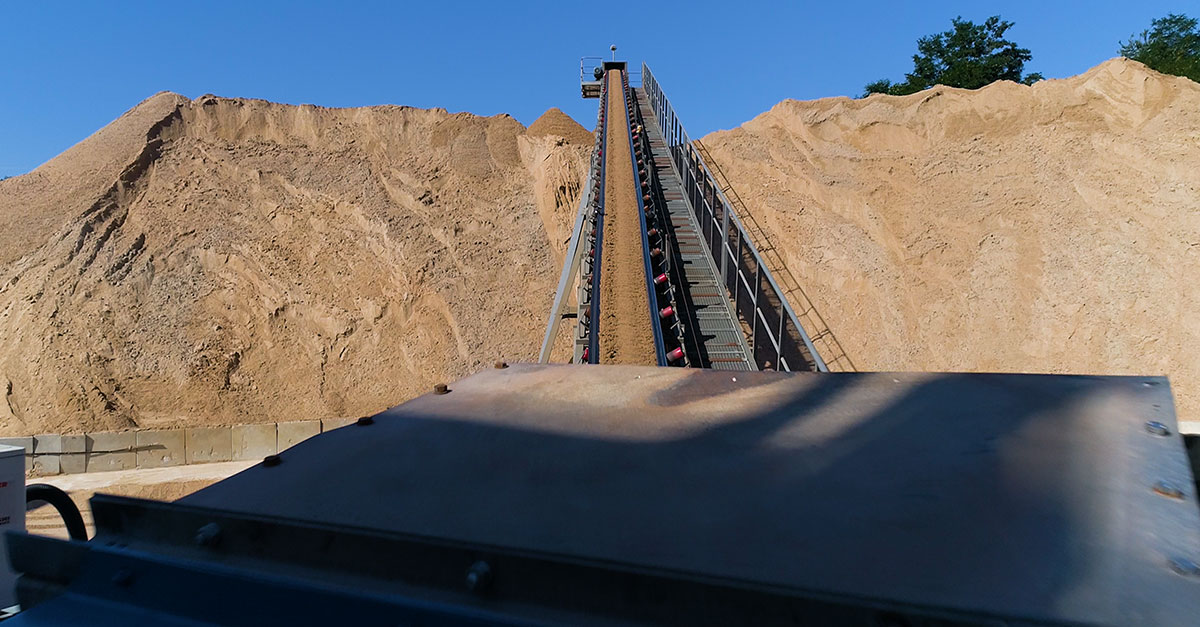
Potential savings through readjustment and low maintenance
For optimum performance, in order to maintain significant savings in water and space for overburden, the centrifuge must be constantly adjusted according to the consistency of the sludge to be dewatered. At the heart of this is the energy-saving Flottweg SIMP drive. The SIMP drive controls the differential speed between the decanter bowl and the internal screw according to the prevailing screw torque. The drive shaft of the gearbox is operated by a frequency-controlled motor, which allows the speed to be optimally adjusted. A second (frequency controlled) motor drives the decanter drum so that the mass moment of inertia to be overcome and regulates the bowl speed as required. Changes in the feed have an impact on the screw torque, since the screw must convey different amounts of solids which leads to different loads. The adjustment of the differential speed can be accomplished very easily and quickly with the SIMP-Drive, thus ensuring a consistently high dewatering of the sludge.
The SIMP drive and other components of the machine ensure that Reithelshöfer can calculate with very low maintenance costs. The closed system, which is designed for maximum load, runs autonomously and is largely maintenance- and wear-free.
"Flottweg's decanter centrifuge has been in use at Reithelshöfer for many years now. The investment has paid off many times over in terms of water savings alone. And despite the harsh conditions and continuous use, the centrifuge has performed its duties without complaint to this day. Even during maintenance, there is not much more to do than occasionally changing a set of V-belts and replenishing oil for central lubrication. The decision to use Flottweg decanter centrifuges has more than paid off for us", concludes Stefan Köhn.
About the Author
Nils Engelke
Nils Engelke is PR and Communications Manager at Flottweg SE
Watch the whole video

Want to learn more about our solutions for the treatment of sand washing water and gravel water?
Talk to us or write us!