2024-04-18
Solving Water Problems for Mines & Quarries - Utilizing centrifuge technology with a clarifier and polymer dosing station
As mines and quarries age, miners and operators are faced with water problems resulting from their washing and processing of product. These problems include a shortage of pond space, needing to mine under their existing ponds, shortage of water due to restrictions, specification limits on water intended to be returned to ground water, or even too much water contaminated by clays and ultra-fines.
The traditional solution has been the use of filter presses and/or settling ponds. This technology not only requires significant capital investment, but comes with a large footprint, requires constant operator presence, and has an ongoing operating expense associated with filter media. Presses and ponds are not portable, and associated civils / structure costs add to CAPEX. Alternately, simply sending the tailings to a pond is not preferred as it quarantines significant mine property.
A reliable, cost-effective alternative is explored here by candidly reviewing two trials of a pilot plant comprised of a clarifier/ polymer dosing unit and a decanter centrifuge that is specifically designed to withstand the rigors of a mining application. The pilot plant ran in parallel with an equivalent size filter press in one operation for a week, and in a separate location for a further week. Both tests showed impressively dry solids, minimal polymer use, and clear centrate liquid.
Introduction
During July and August 2022, pilot operations were run on two separate, independent sand and gravel washing plant sites in Southeast Wisconsin. Site One was at the Lisbon Pit of Lannon Stone Products, Inc. in Sussex WI and is referred to herein as “Lannon.” Typical of the region, the mine site has the usual glacial till mix including sediments, clays and boulders covering the region’s dolomitic limestone. The limestone contains varying quantities of chert and clays.
The Lannon mine produces a dimension building stone as well as sand and gravel. The gravel ranges from riprap to pea gravel and crusher run. The sand is graded into various application grades, i.e., Washed Concrete Sand, Mason Sand, Bedding Sand, Golf Course Sand, and Ultra-fine Washed Sand. Lannon sends their used wash water to their clarifier. It is dosed with polymer by a Clearwater Industries Inc. dosing station, and then allowed to settle out in the clarifier.
The clarifier overflow is sent directly back to the wash plant, and the clarifier underflow is sent to one of two routes. Almost half of the underflow is sent directly to their new 2 meter x 2 meter chamber filter press, and the balance is diverted to their traditional settling/storage ponds. It was this same diverted underflow that provided the feed for the centrifuge.
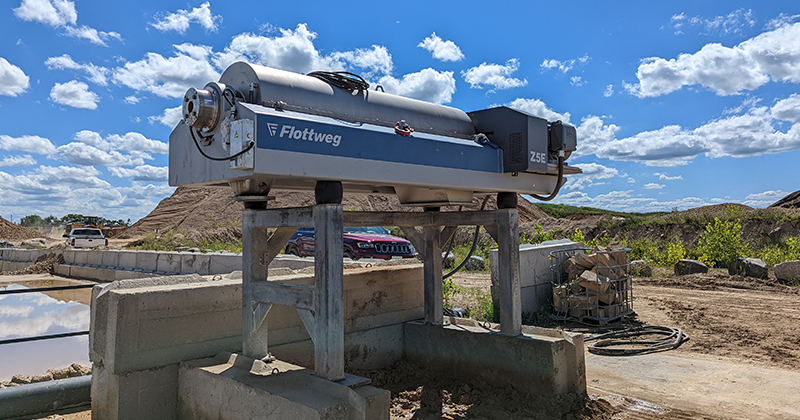
Site Two was at Tri-County Paving, Inc.’s Arlington central wash facility in Arlington WI, and is referred to herein as “Tri-County.” This plant acts as a general receiving, storage, blending and washing plant for multiple quarries and mines—both within Tri-County Paving’s operations and without. Consequently, the mineral range will be somewhat broader than at Lannon, but the regional geology dictates that the basic mix of moraine overlay covering dolomitic limestone still makes up most materials processed.
Sophisticated blending and loading equipment at Arlington allow Tri-County to offer their customers products to very exacting specifications with tight tolerances, from this facility. Water from the sand wash plant is again treated by a Clearwater Industries polymer dosing unit before being sent to the Clearwater clarifier. Water recovered as overflow from the clarifier is returned to the wash water holding pond, while the underflow is sent directly to one of two settling dams to percolate out the excess water. Once again, the clarifier underflow was tapped into to provide the input feed for the centrifuge. This was a much higher percentage solid feed than the Lannon site (typically close to 55% mass DS).
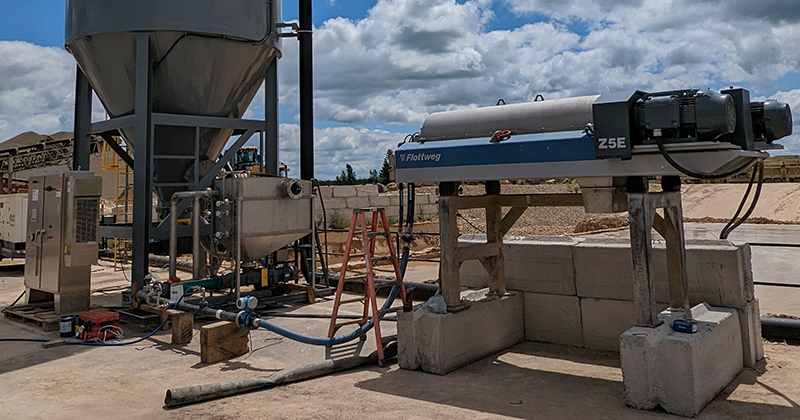
In both cases (Lannon and Tri-County), the same need for separation existed—the used sand wash water required to have the clay and ultrafine sediments removed so it could be reused. All sand is washed in the wash plant, with the expected resultant wash water now contaminated with organic material, blasting residue, clays, and ultrafine particles.
This contaminated water could not be economically stored in ponds for evaporation, and the ponds used space that could be more profitably used for future mining. Further, the water could not be returned to groundwater sources in its current form. Also in both cases, the mine owners selected a clarifier fed by a Clearwater Industries polymer dosing unit to provide accurate flocculent dosing.
Purpose of the Pilot Trials
The main purpose of the pilots was to illustrate that combining a centrifuge with a suitable clarifier and correctly calibrated polymer dosing station can successfully
- recover the wash water for reuse,
- produce solids that are dry enough to be handled by load-out as opposed to requiring pumping,
- save or entirely obviate the need for settling pond space, all while
- running economically with minimal supervision.
The pilot unit was brought up to optimal operating performance within a few hours of installation in both trials, exceeding the test target parameters. Opportunity to test various scenaria using differing feed rates and centrifuge bowl and scroll speeds was taken. This was done to ascertain whether various optimum feed / differential speed combinations between centrifuge bowl and scroll rpms could successfully be achieved.
Variations in polymer dosing were also investigated to confirm if there were more than one optimum production setting for each volume / speed scenario. Clarity of the resultant centrate (liquid discharge) and dryness of solids (DS) produced was measured against the input feed at each setting. Both the clarifier’s dosing station and the centrifuge can be rapidly recalibrated, allowing for us to run 18x separate “what-if” scenaria at each location.
Methodology
The Flottweg model Z5E-4/451 decanter centrifuge selected was equipped with a mining-state wear package to ensure that wear on the bowl, scroll and all entrance and exit points of the unit are protected against the sliding wear that accompanies the typical mining material found in a clarifier’s underflow.
The pilot tests included the decanter centrifuge, its steel elevation stand, and it’s control panel. It also included a feed pump from the OEM’s warehouse, which came complete with a small feed tank. The feed pump is important to maintain a positive pressure on the feed stream. The small feed tank (although not usually required for trial purposes) was handy in that it had top access and was convenient for the team to monitor the feed visually, confirming the readings the density meter was showing.
The feed stream to the centrifuge was fitted with the following live inline instrumentation: -
- a density meter recording the percentage of suspended solids of the input feed,
- a volume meter recording the US gallons per minute of the total feed stream, and
- a volume meter recording the US gallons per minute of polymer solution being fed into the feed stream. This last line was also monitored by the Clearwater Industries Inc polymer dosing unit, which very accurately dispensed the polymer to this line and thus into the feed stream.
The centrifuge’s control panel is connected to all instrumentation and monitors all aspects of operation. Immediate and automatic adjustments are made to account for changes in volume or density input feed – the master controls will select any needed changes in rpm of bowl and/or scroll, also their differential speed, as well as the quantity of polymer dosing to maintain steady-state output. Bearings are also monitored for any vibration changes, as is electrical feed.
Any loss of power will have the centrifuge automatically cut input feed and drain the bowl of solids. Resumption of power at any time will have the unit automatically come back to steady production state, no matter which part of the powering-off cycle is interrupted.
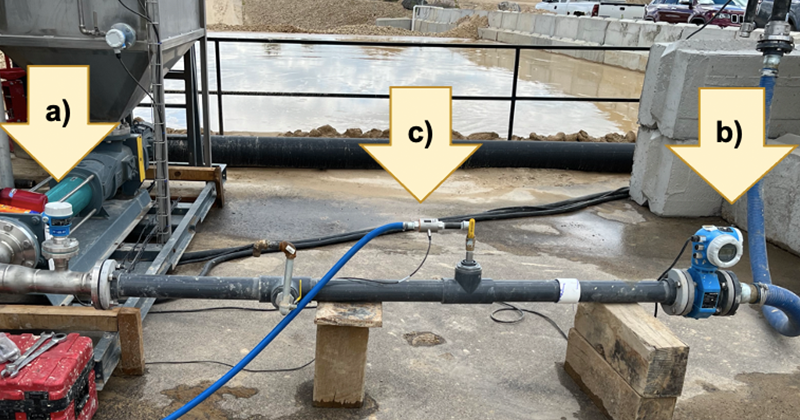
Analysis
A field lab was set up at each site to analyze Dry Solids (DS) for the feed, centrate and cake samples generated. Duplicate samples were also taken for analysis at the Flottweg laboratories, which conducted additional analysis including Total Suspended Solids (TSS) of feed and centrate samples. A sample of feed and centrate were sent to Clark Testing laboratory for particle size distribution analysis in the USA for the Tri County trials; and were measured by Flottweg’s own lab in Germany for the Lannon trials.
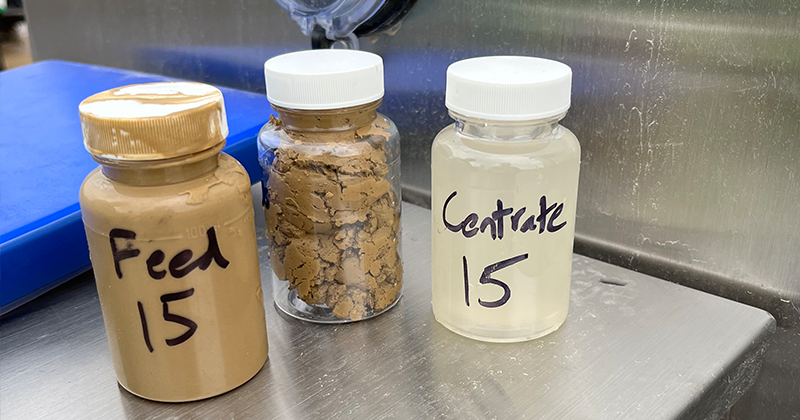
The underflow was fed out of the clarifier into a simple holding tank to allow the operator to visually inspect the feed – again, this tank is not normally required but chosen for the pilots simply because the tank was available on the feed pump skid. The contents of this holding tank were then continuously pumped out of the tapping point on the line. Feed pressure was negligible, no more than one or two bar (15-30 psi) positive pressure was applied to ensure the centrifuge was not starved of input.
The centrifuge discharges both the solid & liquid streams by gravity. Periodic sampling of the feed flow, the solids and the centrate produced were taken at the appropriate significant points of the trials. Samples were also sent to outside laboratory to obtain particle size distribution (PSD) data as below:
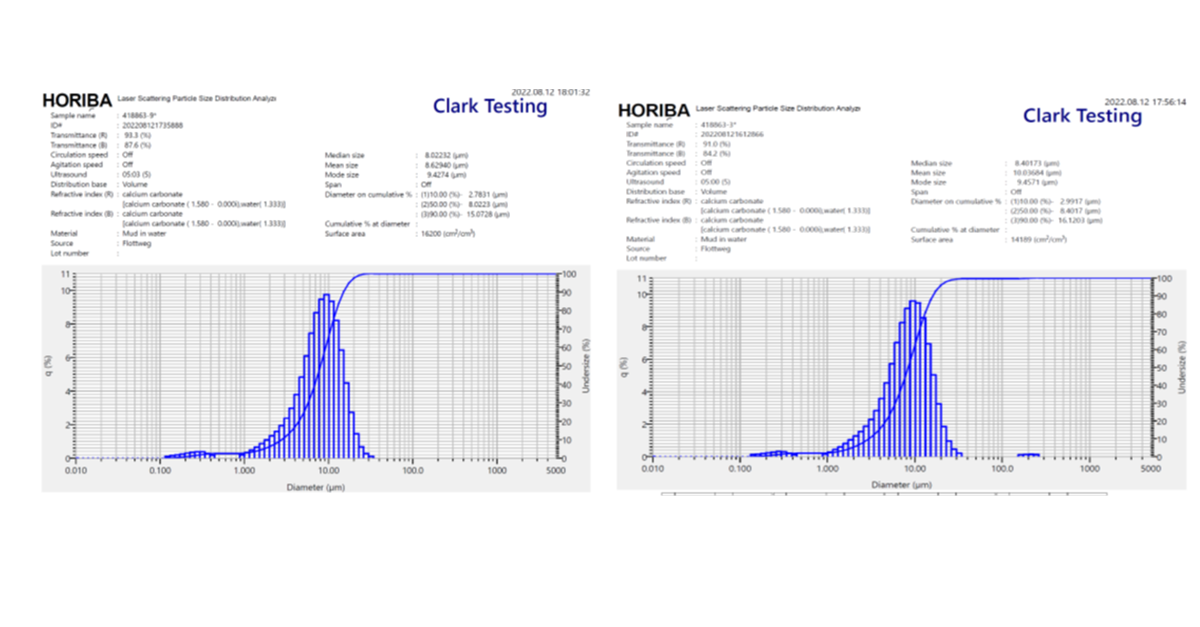
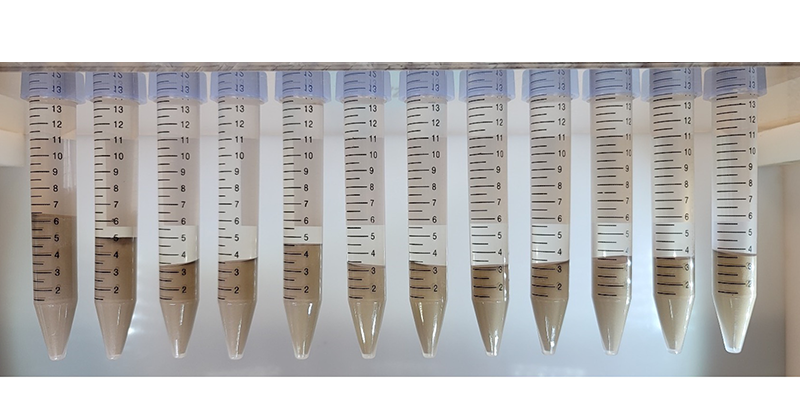
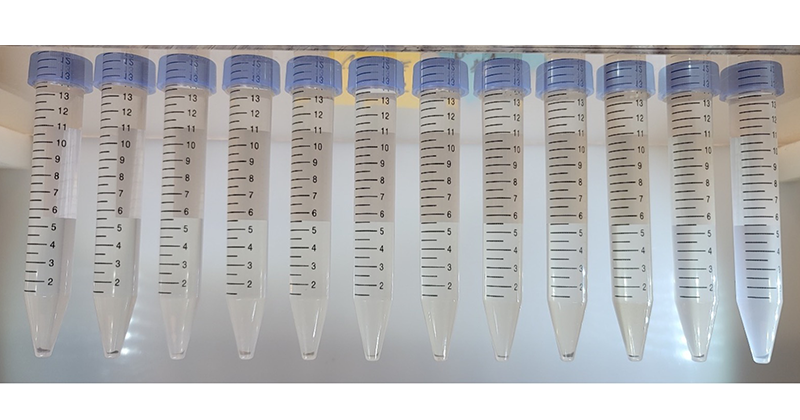
Polymer Preparation
Polymer was prepared using a Clearwater polymer preparation system. The dry polymer used was CW95V at Tri County and CW16 at Lannon. A polymer solution with an active concentration of 0.25% was prepared and used throughout the pilot test. The consumption of polymer was then calculated based on the flow rate of polymer solution and the dry solids flow rate of feed. The units for polymer consumption are given as pounds of active polymer per dry ton of solid feed (lb. ap/dry ton).
Quality of Separation
The quality of separation is evaluated by the suspended solids recovery, the percent total solids in the dewatered cake and the polymer consumption. Adjusting operating parameters will determine the quality of these criteria. The quality of the solids recovery can be evaluated visually. This rapid feedback allows for optimization to focus on generating the driest possible solids with acceptable centrate.
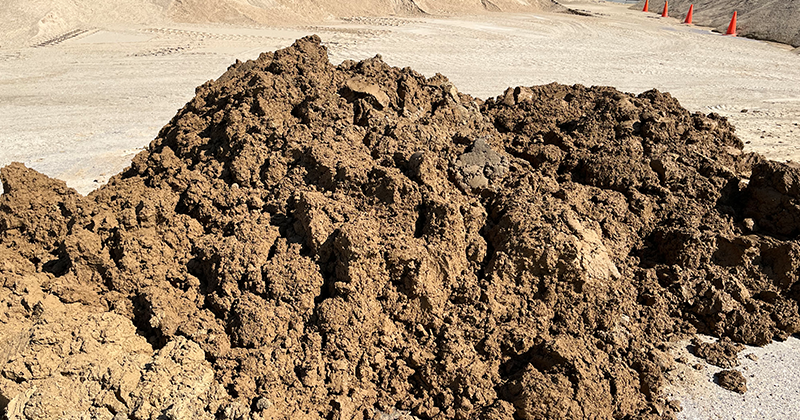
Results
The ranges of the parameters and achieved performance are shown in Table 1 and 2. All individual trial results are found in the appendix. Note that Trial 8 at Tri County had visibly poor centrate, and Trial 13 at same site showed an error on the DS reading and samples were not taken.
Table 1. Ranges of Operating Parameters.
Bowl Speed / Acceleration | 1292 - 1838 | rpm |
494 - 999 | x g | |
Feed Rate (min-max) | 26 - 90 | gpm |
1578 – 18,739 | dry lb/h |
Table 2. Ranges of Achieved Performance.
Centrate | 0.040 – 0.221 | % TS |
0.001 – 0.155 | % TSS | |
Cake | 69.3 – 77.1 | % TS |
Recovery (TSS) | 99.9 - 100 | % |
g-Force
The impact of g-Force in performance is examined by adjusting the bowl speed while maintaining constant operating conditions and parameters. The torque is subsequently adjusted to achieve the driest cake. The cake solids ranged from 69.3 – 77.1% mass TS with drier cake being observed at higher g-Force. Results are shown below:
Polymer Dosing
As the polymer binds the solids together, the amount of polymer being dosed will influence the achievable separation. A polymer curve can be established by varying the polymer consumption while maintaining constant operating parameters and conditions, which can be used to find an optimal polymer dosing window. The optimal polymer dose was found at 0.20 – 0.27 lb ap/dry ton, while there was a small reduction of achievable cake dryness after the polymer dosage was increased to over 0.35 lb ap/dry ton.
This very low volume of polymer needed to consistently produce the Dry Solid % achieved was a welcome confirmation that the usually very much higher dosage rates used in the industry at assist separations was overkill, and counter separation if over-dosed. Careful trial at initial installation will provide excellent separation at low dosage.
Conclusion
To save up to 90% pond space or even more, a decanter centrifuge combined with a clarifier / polymer dosing unit is a very affordable and effective solution. As much as 90% of process wash water can be recovered. Spadable solid material suitable to be handled by conveyor or truck is produced. Recovering reusable water from the wash plant process in sand and gravel with a suitably wear protected centrifuge decanter in conjunction with a clarifier / matching polymer dosing unit works extremely well. The results achieved on these U.S. trials are 100% in correlation with results at current multiple installations in Europe.
Almost all (+99.9%) of suspended solids are removed from the wash water, and the solid output is spadable and can be removed by conveyor belt, screw conveyor or truck. Typical dryness of solid of ≥ 69% to as high as 77% (mass DS) can be expected in steady state.
Polymer dosage required to assist separation was minimal. Usual expectations are 500g to as much as 2 kg per dry ton is the norm. The centrifuge was able to achieve solids recovery +99.9% and dewatered cake with 69% to 77% TS at polymer dosages of 0.17 – 0.44 lb. ap/dry ton (77g - 199g per dry ton). Consistent feed rates of between 26 to 90 gpm (98 to 341 lpm) were achieved. This translates to between 5.9 and 20.4 m³/hr.
The centrate (liquid) output is clear and completely reusable as wash plant water, saving the mine as much as 90% of their wash water needs. Electrical demand is consistent and predictable. Very little operator supervision & periodic maintenance is required, and the system is fail-saved to ensure no negative impacts of sudden surges of solids in the feed, feed failure or power interruption.
Eric Gentis, Flottweg Separation Technology and Andrew Gralton, Clearwater Industries Inc.
[Additional Author Contributions] Stefan Ecker, Joe Lamb, Terry Ostrom, Martin Eckl, Robert Klug, Tony Kramer and Dustin Miller of Flottweg Separation Technology and the owners and teams at Lannon Stone Products, Inc. of Sussex WI, and Tri-County Paving Inc of DeForest WI contributed to this report